Recondition Service
All Kinds of 2 & 4 Stroke Diesel Engine
- RECONDITION / OVERHAUL / REPAIR
Cylinder Cover / Head, Exh. valve Spindle & Bottom Piece, Piston Crown, Rod, Skirt and Etc.
- CHROME PLATING
Ring Groove for Piston Crown, Stem Part for Exh. valve Spindle, Shaft and etc.
- HVOF COATING
Piston Rod, Exh. valve Spindle and Cage
- OTHERS
FIVA valve, FO Parts (Plunger & Barrel, Spindle Guide, Nozzle and etc.)
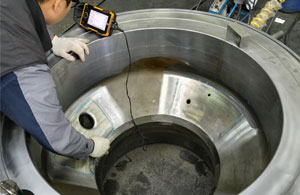
- Cylinder Cover - 2 stroke
-
1) Cleaning and initial inspection with hydro-pressure testing & PT.
2) Preheating of the whole cylinder cover in the electro-furnace and keeping the temperature with gas burner during welding.
3) Welding/Machining/Boring/Drilling/Re-tapping of weardown, corroded and/or damaged parts.
4) Post weld heat treatment in electro-furnace.
5) Machining of the exhaust valve seat & cooling jacket contacting surface.
6) Lapping at fuel injection valve hole, starting air valve pocket, safety valve pocket.
7) Final inspection with hydro-pressure testing & PT, cleaning, painting.
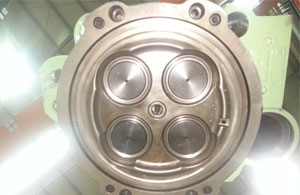
- Cylinder Head - 4 stroke
-
1) Dismantling of all accessaries.
2) Chemical cleaning and initial inspection with hydro-pressure testing & PT.
3) Renew damaged/worn-out parts.
4) Grinding & lappinng of Exh/intake v/v & seat
5) Painting & reporting
6) Assembling of the all parts.
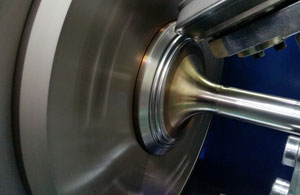
- Exh. v/v Spindle - 2 stroke
-
1) Cleaning and initial inspection with dimension checking & penetrant testing.
2) Annealing in elecric-furnace prior to repairing.
3) Machining of the seating surface and penetrant testing.
4) Welding & Machining of the seating surface.
5) PWHT in electric-furnace
6) Final inspection with dimension checking & PT.
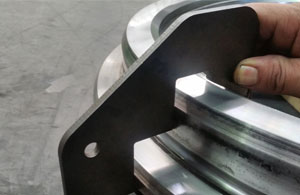
- Bottom Piece - 2 stroke
-
1) Cleaning and initial inspection with dimension checking & penetrant testing.
2) Machining of the seating surface.
3) Final inspection with dimension checking & penetrant testing.
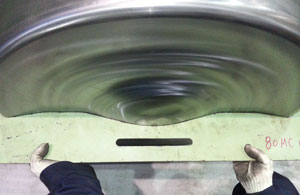
- Piston Crown - 2 stroke
-
1) Cleaning inner & outer surface of the piston crown and initial inspection with dimension checking & PT.
2) Machining ring grooves prior to welding.
3) Preheating & Build-up welding on the all ring grooves.
4) Welding & Machining of the "O" ring contacting surface on the cooling space.
5) Post weld heat treatment in electro-furnace.
6) Machining ring grooves for chrome plating.
7) Chrome plating on the all ring grooves and polishing to the original specifications.
8) Final inspection with dimension checking & PT.
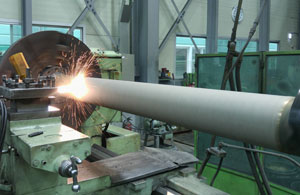
- Piston Rod - 2 stroke
-
1) Cleaning and initial inspection with dimension checking & penetrant testing.
2) Grinding at the whole sealing surface.
3) Skimming of the piston crown contacting surface.
4) Final inspection with dimension checking & penetrant testing
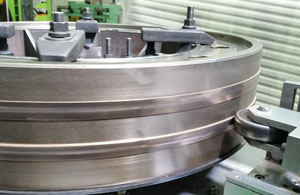
- Piston Skirt
-
1) Cleaning inner & outer surface of the piston skirt and initial inspection with penetrant testing.
2) Machining of the groove for copper band.
3) Newly inserting copper band and machining to the original specification.
4) Final checking with penetrant checking.
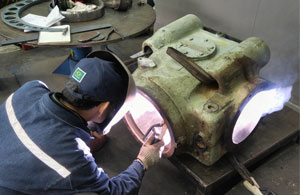
- Exh. v/v Cage
-
1) Dismantling of all part for exhaust valve cage assemble.
2) Cleaning & Initial inspection with hydro pressure & PT for exhaust valve housing
3) Replacement of the heil coil for Exh. Gas outlet side flange.
4) Machining at contacting surface of the Exh. valve seat.
5) Assembling of all part for Exh. valve housing assemble.
6) Cleaning & Painting.
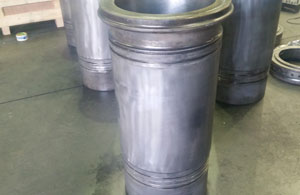
- Cylinder Liner
-
1) Cleaning inner & outer surface of the cylinder liner and initial inspection with dimension checking & penetrant testing.
2) Honing at liner inside.
3) Final inspection with dimension checking & penetrant testing.
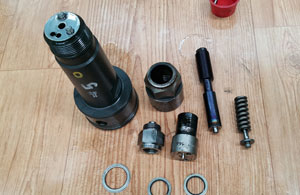
- Fuel Injection Parts - 2&4 stroke
-
* Spindle Guide
* Non Return v/v
* Puncture v/v
* Suction v/v
* Nozzle Tip …. and etc.
1) Grinding of the spindle.
2) Lapping on the seat face of the spindle guide.
3) Grinding of the neddle
4) Injection pressure & leakage testing.
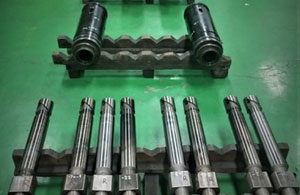
- PLUNGER & BARREL - 2 stroke
-
1) Cleaning and initial inspection with measuring.
2) Horning of the inner surface of barrel.
3) Newly manufacturing of the plunger.
4) Final inspection and clearance checking between plunger and barrel.
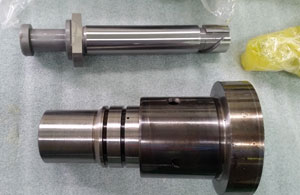
- PLUNGER & BARREL - 4 stroke
-
1) Cleaning and initial inspection with measuring.
2) Horning of the inner surface of barrel.
3) Newly manufacturing of the plunger.
4) Final inspection and clearance checking between plunger and barrel.
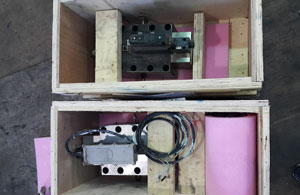
- FIVA V/V COMPLETE
-
1) Disassembly and cleaning with the specific machine
2) Visual inspection and dimension check
3) Measurement of clearance between main housing and spool
4) Replacement of proportional valve and inductive sensor
5) Reassembly with new o-ring kit
6) Calibration and performance test
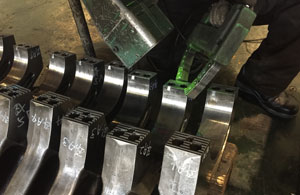
- Connecting Rod - 4 stroke
-
1) M.T & Dimension check.
2) Crack V-out & M.T Check.
3) Serration lapping.
4) Big end pocket boring.
5) Bending & Twisting inspection.
6) Small end bush renewal.
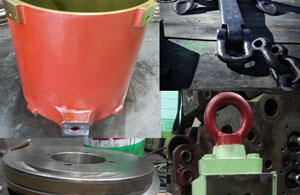
- Others
-
* Air / Oil Cylinder
* Hyd. Top Bracing Device
* Air Compressor
* Heat Exchanger
* and etc.